Progress is being made every day within the trucking industry to make operations more efficient, profitable, and secure. Technology has played a significant role in these advances, making information considerably easier to access and use. Whether it’s technological innovations employed in our offices, repair shops, or trucks, new software is transforming the industry. One sector that has particularly progressed is fleet maintenance programs.
What is preventive maintenance?
In its simplest terms, preventive maintenance (PM) is an approach to equipment upkeep that focuses on preventing issues rather than repairing them. This method helps to avoid breakdowns by regularly inspecting equipment and servicing or replacing parts before they fail.
Routine maintenance may seem like a high-cost habit to implement, but planning reduces the chances of unforeseen downtime which is ultimately more costly for maintenance teams and facility managers. Consider the increased costs of emergency roadside service, the additional demands on administrative staff when loads are sidelined, and the potential loss of customers. When you consider those costs, it’s clear that PM is a safety, efficiency, and profit-maximizing plan.
An effective routine can be based on calendar days, hours of service, or mileage. While maintenance software isn’t a necessary element of PM, an effective plan is informed by real-time data which is typically collected by tools like CMMS software. So, while it’s not mandatory, it can make staying on top of multiple units much more manageable.
Why choose preventive maintenance?
Despite a decade-long push by industry experts to promote the benefits of preventive maintenance in the trucking industry, research shows that a reactive or “run-to-failure” approach is still a leading maintenance strategy. As of 2020, 60% of companies were still carrying out reactive maintenance.
Any time a unit in your fleet has unexpected downtime for maintenance, there are costs involved. If you’re worried that replacing parts too early is the equivalent of throwing money away—you need to consider whether the additional cost of downtime and emergency repairs outweigh the savings of running it until it fails.
Even if you set aside the potential costs that are harder to project, such as lost revenues or a loss of customer confidence, there are plenty of concrete numbers that show how reactive maintenance costs more than it saves. Factors like towing, third-party labor, and mark-ups on replacement parts make repairs more expensive out on the road than they are in your shop.
It takes more than an annual DOT inspection and pre-trip check-ups to keep a commercial vehicle running. It’s one thing to keep your fleet running, but it’s another to keep it running efficiently. To eliminate breakdowns, minimize downtime, and maximize fuel efficiency, thorough maintenance inspections need to be done periodically. Preventive maintenance will deliver across-the-board benefits that improve your bottom line.
Cut costs with a preventive maintenance plan
The idea of implementing a preventive maintenance program can seem especially challenging for a small or mid-sized fleet. In addition to budgeting for routine maintenance, fleet managers need to account for software solutions that allow them to keep up with competitors and easily manage their PMP.
The combination of upfront costs and adopting a whole new program is often what prevents fleets from switching to preventive maintenance, but in the long run, they’re spending more on maintenance with a reactive approach.
Reactive maintenance introduces high costs such as sudden third-party labor, rush parts, and towing. These are some of the biggest financial downsides of a run-to-failure structure. The many benefits that preventive maintenance brings to your fleet will help you reduce costs and increase efficiencies in ways that will pay for the initial investment many times over.
Optimize scheduling
In the trucking industry, one thing is clear: downtime is not profitable. The negative impacts that downtime has on your fleet can be long-lasting and tough to recover from.
Scheduling preventive maintenance maximizes both driver and maintenance technician productivity by establishing a set amount of time equipment will be off the road being inspected.
When vehicles unexpectedly break down, there’s no telling where the nearest repair shop is or how long the service will take. This takes vehicles and staff off the road, leading to messy last-minute rescheduling and ultimately a delay in delivery.
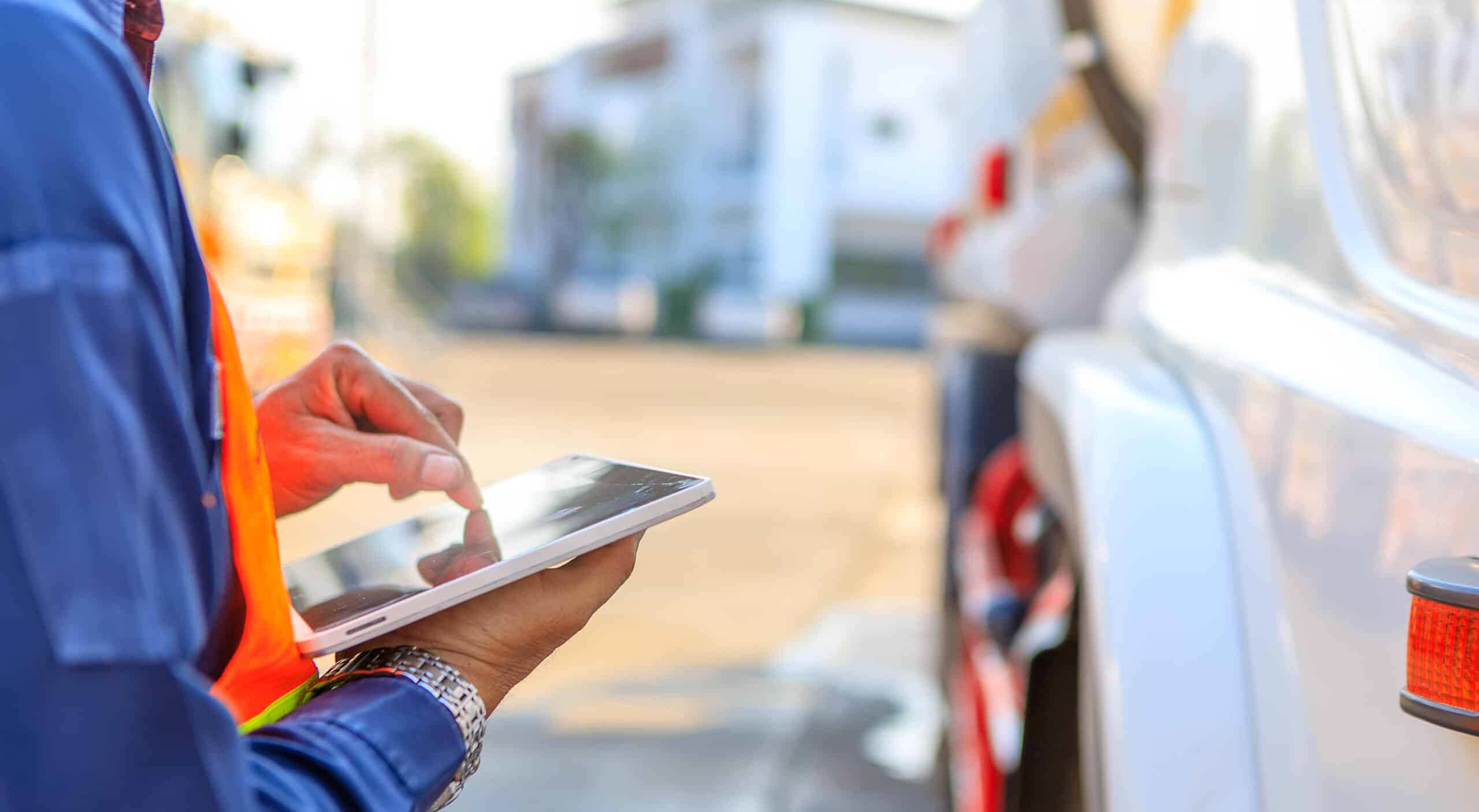
Improve client relationships
Happy customers are priceless. The easiest way to upset your clientele is by breaking guarantees. Even if a client is understanding when it comes to a delay, it’s a bad habit to fall into and can hurt your company’s credibility.
Testimonials are the driving force of any successful, trusted organization and are essentially a free advertising channel. Losing clients can cost your fleet far more than the price of a PMP, not to mention emergency repairs surpass all options when it comes to cost. Avoiding negative reviews by providing timely, reliable service will promote growth for your fleet.
Enhance asset performance
When you follow a preventive maintenance routine for the lifetime of a unit, not only will it operate more efficiently, but it will also retain a higher value when it comes time to sell.
When you add up the savings over the life of a single unit, they are considerable. When you multiply lifetime savings by the number of units in your entire fleet, the difference preventive maintenance makes for your bottom line starts to come into focus.
How can preventive maintenance software help manage your program?
With today’s advances in the automotive industry, equipment is constantly developing. With electronic control modules (ECMs) and electronic logging devices (ELDs), your fleet’s PMP can now incorporate information from both drivers and units seamlessly. Most preventive maintenance software can use the information from these sources to generate work orders and schedule shop time.
Preventive maintenance software can also be integrated with your spare parts inventory, making it easy to determine if new parts are needed so technicians are ready to get to work as soon as the unit gets to the shop.
Using preventive maintenance software doesn’t just streamline the operational aspects of your PMP. It will also make capturing, tracking, and documenting the program’s output more efficient. Between generating reports and creating a hub for fleet data history, the software makes managing your current budget and anticipating future needs much simpler.
The benefits of a preventive maintenance program aren’t a luxury that only big national fleets can afford anymore.
At Fleetpal, we work hard to bring small and mid-sized fleets the tools that they need to take advantage of the technological advances that the industry has made. Contact us today to learn how our maintenance management software helps fleet managers, maintenance managers, and suppliers collaborate.
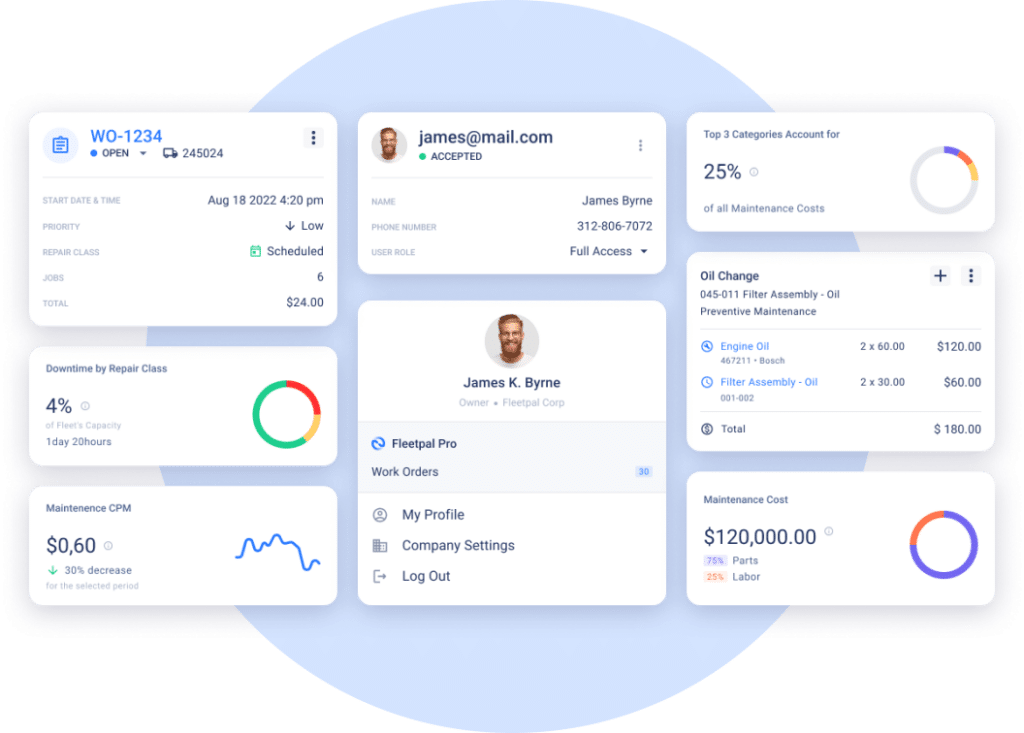